“Hi there, I have been searching for an actual wooden case for quite some time. I just want to make sure that this is actual wood”
-Email to KerfCase last week. Trust me, we make real wood cases! Check out the video below to see the proof.
WHAT IS A REAL WOOD PHONE CASE?
Being in the wood phone case business is a tough gig sometimes. We make a high-quality, labor-intensive product, but our marketplace is littered with cheap imitators. Do a search on Amazon or Google Shopping for “wood iphone case” and you’ll see what I mean.
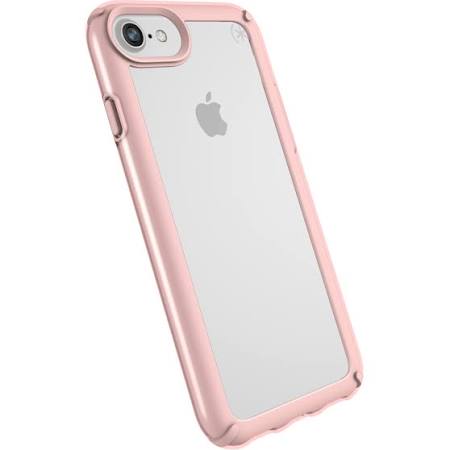
As we’ve previously explained, there’s not exactly a standard definition for what constitutes a wood phone case. Unlike Scotch Whiskey or Belgian Chocolate, which need to meet distinct guidelines in order to be advertised with those names, you can put a piece of wood on top of a mass-produced case, or even order a wood-and-plastic case overseas and sell it at a massive profit, and get away with it. In an unregulated market, it’s up to the consumer to be extra sure they’re getting what they’re paying for, and for companies like ours to advertise our product in a way that emphasizes its authenticity.
That email up at the top of the page, which we received not too long ago, shows us that we need to do more to show you how we differ from the competition. So today, we’ve decided to lift the veil on some of our production processes to leave no doubt to you, dear reader, that we are the real deal.
THE CNC REVOLUTION
You may have heard the abbreviation CNC before. It’s short for Computer Numerical Control and describes a type of industrial equipment. A CNC machine is not operated by hand; it takes a type of tool, such as a router or a laser cutter, and gives control of it over to a computer that feeds it a series of instructions.
The magic of a CNC machine is simple: as a human operator, you simply give the machine a program, press a button, check your Facebook for a couple minutes, and return to find that a complicated task has been performed automatically and with a high degree of precision. If you know how to use one, you can perform a staggering variety of tasks with one machine.

We’re in the midst of what some are calling the Maker Revolution, where for the past decade there’s been an explosion of small businesses selling high-quality crafts. Beyond platforms like Etsy that give individual sellers and boutique shops a venue for sales, what’s driving this trend is the miniaturization of CNC machines. Once, owning a robot that could spit out a finished part would put you back a couple million dollars, but now there’s a thriving industry of companies that make 3D printers, laser engraving machines, and carving stations that are priced for small businesses or even crafty consumers! We should know, since at our last count, we are the proud owners of 8 different CNC machines of varying shapes and sizes.
Today, I want to show you our Shopbot. We’ve owned this helpful robot for about a year now, and it is the beating heart of KerfCase. Every case we make starts its journey on it.
This machine takes wood billets, or boards of a uniform length, width, and thickness, and turns them into a basic case shape. Beneath the dust collector, a spinning router bit moves in a pre-programmed path, systematically carving out the inside of the case, then the camera and fingerprint holes, and then the outer edge. Check out this time-lapse video of a Google Pixel case being carved from a rosewood billet:
I hope you have as much fun watching this time-lapse as I had making it!
Pretty cool, huh? To make this video, I removed the dust collector and vacuumed up the sawdust by hand; ordinarily, the orange hose you see in the photo is connected to a shopvac that does all of the vacuuming automatically. What was once a nigh-impossible task for a person to do by hand is done in about 10 minutes by a very predictable process. As long as we perform routine maintenance on our Shopbot, and pay close attention to certain dimensions of the final product, we have a very reliable and quick first step of our assembly line!
NOT THE EASY WAY
This work didn’t come easy. There’s a strong Do It Yourself streak built into operation of CNC machinery, and owning the equipment isn’t enough. You have to teach it what you want it to make. Fortunately, our deep ties to the Pittsburgh maker scene have given us the expertise we need to program our machines to do the specialty work we need them to do. In the video, every sweep and pass the router bit does is to ensure that the final product is as predictably shaped, and undamaged from the carving process, as possible. This optimization work is constantly evolving, and gets better and easier with every case we design!
If you’re paying attention to the video, you can see our second step as well. After we remove the case from the ShopBot, we take its measurements and install a thin strip of wood veneer on the inside edge. This custom piece serves two purposes: It provides additional structural support for the case, and the groove that runs through the middle holds the phone snug! This creates the secure - but easy to install - friction fit that sets our cases apart from so many of our competitors.
We’d love to show you the whole process, but we’ve gotta keep some of the formula secret! I hope you enjoyed this little taste of the Kerf production process, and I hope I’ve convinced you that we use real wood. Let me know if you have any questions by sending me an email, I’m always happy to chat.
Phil Giammattei likes to wear lots of different hats. Formerly employed at Apple, Google and Oracle, he loves applying his technical knowledge to making the best possible custom wooden phone cases. In addition to writing the Kerf Blog, Phil’s duties at KerfCase include customer service, sales, production, shipping and fulfillment, and anywhere else he can be helpful. Reach Out to say hi and find out what choice cuts we have in stock!